当記事のリンクには広告が含まれています
皆さんはFMEAというツールを知っていますか?故障モードとその影響を分析するツールになり『Failure Mode and Effects Analysis』の頭文字をとってFMEAといいます。もともとは航空宇宙産業で効果を発揮したことから、自動車業界でも活用するようになった手法です。
今回はそのFMEAについて、わかりやすく解説をしたいと思います!
こんな方にオススメの記事
- 自動車関係の製造メーカーに勤務されている方
- 設計部門や生産技術部門で業務を行う方(これから行う方)
- FMEAという言葉を始めて聞いた方
- とにかく不良品を低減させたい方
FMEAの歴史
FMEAはもともと航空宇宙産業で用いられ始めたツールです。ロケットを1発打ち上げるのには何百億円という膨大なコストがかかります。何発も試作ロケットでテストできれば良いのですが、そういうわけにもいかないです。
そこで活用されていたのが、FMEA(故障モードとその影響の解析)。事前に予測できるありとあらゆるリスク(故障モード)を分析し、その影響はどういう部分に生じてしまうのかを、台上で検討を重ねてロケットの打ち上げに挑むのです。
今日では自動車産業にも用いられている手法となっており、IATF16949で要求されている事項となります。製品設計と生産工程設計のリスクを分析し、欠陥につながる潜在的要因を排除するために活用されています。自動車は量産されると何百台という車両が世界中に出回るので、設計・開発段階で事前にリスクを排除する事が非常に重要となります。
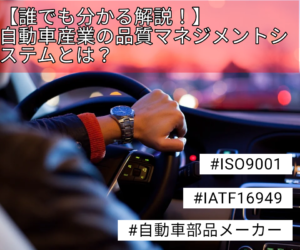
FMEAの種類
FMEAには大きく分けて2つのFMEAが存在します。
- Design-FMEA(設計FMEA、D-FMEAと呼ばれます):製品設計に関するFMEA
- Process-FMEA(工程FMEA、P-FMEAと呼ばれます):製品の製造工程に関するFMEA
FMEAには、設計観点で製品図面や構成等に対して行うFMEAと、生産観点で生産工程の装置や人が行う作業方法に対して行うFMEAが存在します。しかしFMEA自体に縛りはなく、私の経験では総合職のマニュアル作業(例えば、生産依頼や出荷停止指示等)に対してFMEAを行っていたケースも知っています。
その企業が感じる危険な部分に対して、リスク分析を行うのがベストです。
FMEAは何に対して作成すれば良い?
FMEAを作る上で、どの製品に対して作ればよいか疑問に思う方もいるかもしれないので解説します。結論から申し上げるとその会社が区分を決めて作成して良いのですが、一般的には品質特性(品質を構成する要素)が異なればリスクも変わってくるので、モデルや型番別でそれぞれFMEAを作成するのが理想です。
例えば、A社はブラウン管テレビと液晶テレビそれぞれにFMEAを作成しているのに対し、B社はテレビというカテゴリでFMEAを作成しております。どちらも間違いではないですが、ブラウン管テレビと液晶テレビでは構成部品も構造も全く別物であり、考えられるリスクも変わってきます。よって、A社の方が理想のFMEAといえるでしょう。
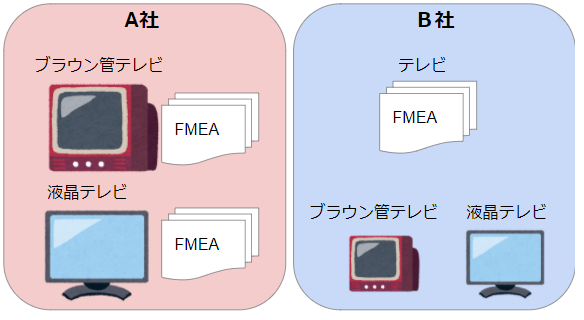
FMEAの作り方
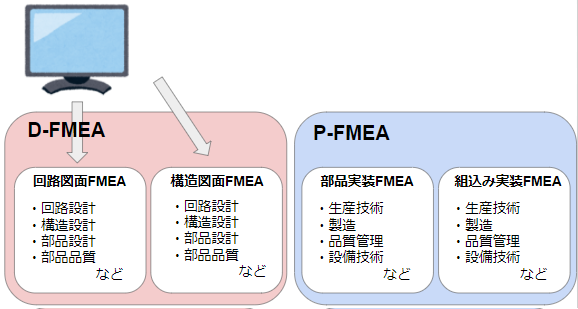
1つの製品を作る場合でも、設計観点でも生産観点でも様々なチームが存在します。各区分に分けFMEAをチームで完成し、最終的にFMEAを繋げることで完成します。

① 故障のモードを入れる
② その故障が製品や顧客に与える具体的な内容を入れる
③ その影響が与える重要度を10段階で入れる
④ 故障が発生する可能性のある原因を入れる
⑤ 故障が発生する発生率を10段階で入れる
⑥ 故障を検出できる可能性がある方法(検査方法)を入れる
⑦ 検査方法から検出率を10段階で入れる
⑧ 重要度③×発生率⑤×検出度⑦ でリスク(RPN)を計算する
⑨ リスクが高い項目の場合、リスクを下げる改善策の内容を入れる
⑩ 改善後のRPNを計算する
ここのリスク(RPN)を数値化することで、リスクの優先度を明確化します。RPNは『Risk Priority Number』の略語で、リスク優先度です。
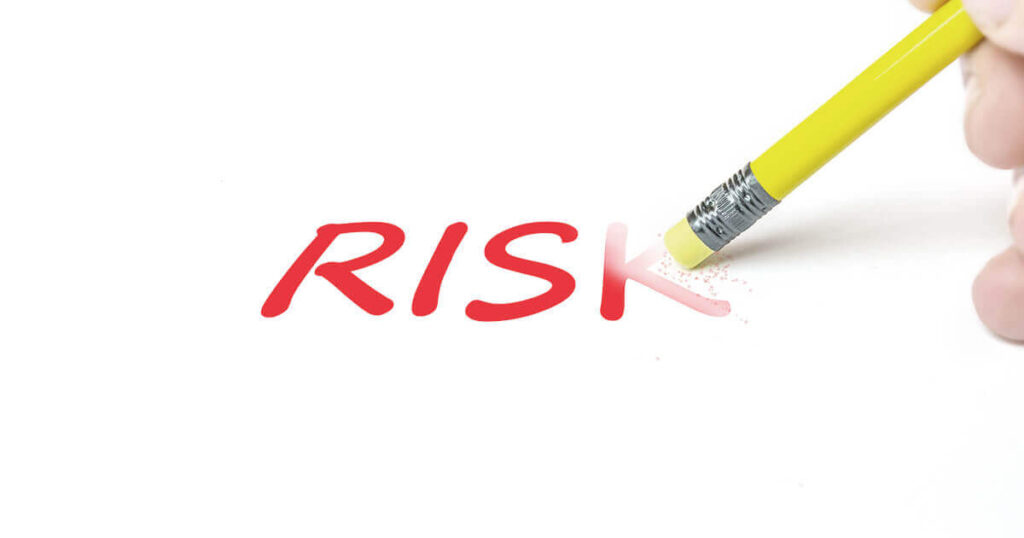
この作業はSTEP1で上げたチーム編成にのっとり行う作業で、この作業がFMEAでは一番重要な作業です。STEP2で作成したフォーマットを利用して、考えられるリスクを洗いざらいにします。作成したフォーマットの故障モード前に項目を追加し、具体例を用いて説明をいたします。

このように、どいった作業が各工程で行われて、その作業で考えられるミスをあげる事で、リスク管理を行います。このリスクをあげればあげる程、良いFMEAになり、それは様々な知見をもった人を集めて作成することで、完成度があがります。
スコアはその企業が定める規定に従い付与しますが、基本的には以下が定義となっています。
影響度の10段階
重要度 | 具体的な内容 |
10 | 機能しない・致命的(人命にかかわる) |
9 | ある条件下で機能しない・潜在的に法規に影響する可能性 |
8 | 機能しない(機能喪失)可能性がある |
7 | ある条件下で機能が低下する |
6 | 機能が低下する可能性がある |
5 | 機能するが、改善が必要 |
4 | 機能するが、改善が推奨される |
3 | 影響ないと判断できる |
2 | 無視できる影響 |
1 | 影響なし |
発生頻度の10段階
重要度 | 具体的な内容 | 頻度の目安 |
10 | 常に発生する | 毎回 |
9 | 頻繁に発生する | 1回/日 |
8 | 発生頻度が高い | 1回/週 |
7 | よく発生する | 1回/2週 |
6 | たびたび発生する | 1回/1か月 |
5 | 低いとはいえない | 1回/6か月 |
4 | 発生頻度は低い | 1回/1年 |
3 | ごく稀に発生する | 1回/3年 |
2 | ほぼ発生しない | 1回/5年 |
1 | 発生しない | 発生しない |
検出度の10段階
検出度 | 検出度の目安 |
10 | 検出することができない |
9 | 検出率10%程度 |
8 | 検出率20%程度 |
7 | 検出率30%程度 |
6 | 検出率50%程度 |
5 | 検出率70%程度 |
4 | 後工程で100%検出できる |
3 | 次の工程で100%検出できる |
2 | 作業中に検出できる |
1 | その時点で100%検出できる |
FMEAを使った再発防止策
IATF16949:2016 10.2.3 問題解決 では不適合が発生した際の是正処置についての要求事項が書かれています。そこで『適切な文書化した情報のレビュー及び必要に応じた更新』と定められ、PFMEAと具体例が書かれています。
不具合が発生した際に是正を行いますが、その不具合が発生してしまった原因はPFMEAでリスクとして抽出できていたのか厳しく問いつめらていました。何故、リスク管理ができていないままFMEAを完成させてしまったのか、FMEAの確認承認プロセスには問題なかったのか等々、再発防止活動の上でFMEAを作り上げるまでのプロセスの是正を行っておりました。
また必ずFMEAの見直しを要求されており、不足していたリスクを再度FMEAに追加し改定しました。FMEAは次モデルを開発するときに、前モデルのFMEAを参考に書き足していくので、次モデルに対する再発防止としても役立ちます。
作るのは大変ですが、作ってしまえば財産となるでしょう!
まとめ
- FMEAは上流工程で事前にリスク管理をするための大切なツール
- D-FMEAとP-FMEAが存在し、それぞれチームを組んで作成する
- 色々な知見者を集め作る事で、リスク抽出の完成度もあがる
- FMEAは再発防止活動でも用いられ、FMEAを改定することで次モデルの開発にも役立てる
- FMEAを作るのは大変だが、作ってしまえば財産となる!
コメント