はじめに
みなさん、QC七つ道具という言葉はご存知でしょうか?
製造業で働かれている方は、よく聞く言葉だと思います。
”データ”には2種類存在します。
一つ目が『言語データ』です。例えば、「デザインがかっこいい」「色がきれい」といった、その製品が持っている特性(性能や状態)を言葉で表現したデータ(情報)のことをいいます。
二つ目が『数値データ』です。「不具合が2つ発生した」「100個ネジを作って平均5cmの長さだった」といったように、数値で表現したデータをいいます。
QC七つ道具は『数値データ』を改善する手法として生まれました。
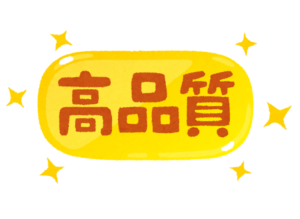
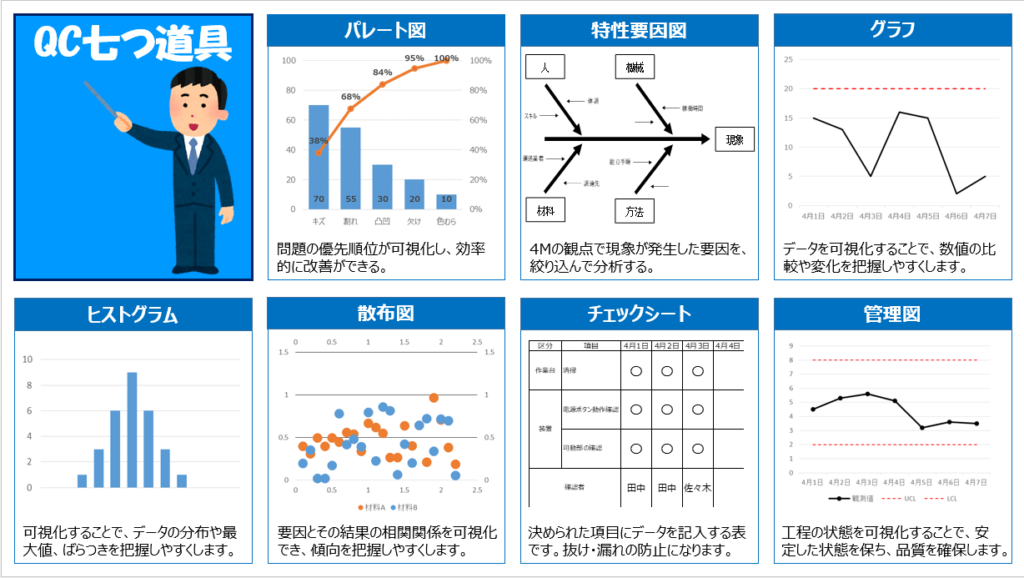
QC七つ道具の用途
はじめに、一例にはなりますが、それぞれのQC七つ道具はどのような用途で使われるのか表で表します。
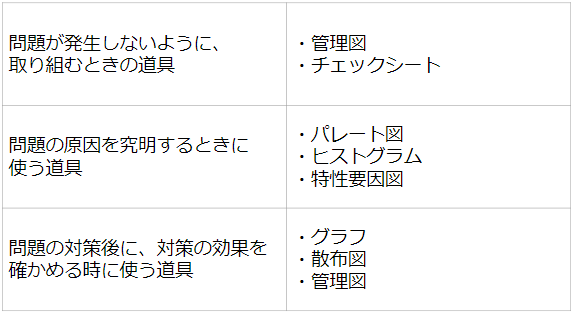
それぞれの概要は以下です。
- パレート図
問題の優先順位を可視化し、効率的に改善ができます。 - 特性要因図
4Mの観点で現象が発生した要因を絞り込んで分析します。 - グラフ
データを可視化することで、数値の比較や変化を把握します。 - ヒストグラム
可視化することで、データの分布や最大値、ばらつきを把握しやすくします。 - 散布図
要因とその結果の相関関係を可視化でき、傾向を把握しやすくします。 - チェックシート
決められた項目にデータを記入する表です。抜け・漏れの防止になります。 - 管理図
工程の状態を可視化することで、安定した状態を保ち、品質を確保します。
では、具体的な事例を交えながらひとつずつ解説をしていきます!
パレート図
例えば、生産した製品で100個の不具合が生じました。
どうやって改善しましょうか?やみくもに一個ずつ原因を探る?
一番効率的なのは、多く出ている不具合の原因をつぶしていくことです。
すべての原因をつぶし込めればよいのですが、時間は有限です。1/100個しかない不具合の原因を改善するより、50/100個の原因をつぶした方が効率的に品質改善に取り組めますよね。
そんな時に使うのが『パレート図』になります。
例えば、目の前に合計185個の不具合品があると想像してください。それらを事象別で分類し、集計しました。その結果が、上図パレート図です。
”キズ” の不具合は全体の 38% を占めるので、この不具合をやっつけてしまえば、約4割も不具合を減らせます!
問題の優先順位を可視化し、効率的に改善ができる手法。それがパレート図です。
特性要因図
見た目の形から海外では Fishbone diagram(魚の骨図)と呼ばれたり、石川さんが考案したことからIshikawa diagramとも呼ばれます。
この図は、事象に対して4Mの観点からどんな要因が影響を与えている可能性があるのか分析する道具です。
ここでいう4Mとは、
(人:Man、機械:Machine、材料:Material、方法:Method)の頭文字をとって4Mといいます。
特性要因図は下図のように表します。
例えば、”キズ” が発生してしまった原因を究明しようとしています。
人が原因となる要因としては、スキルが不足していたり、体調が悪かったりなどで、正しい作業を行うことができず、製品にキズをつけてしまったりするケースが考えられます。
機械では、可動部が強く接触してしまったり、アームが製品を離すタイミングが悪かったり、
材料では、調達先や運送業者の管理が悪かったり、
方法では、作業を行う手順が悪かったり…
などが考えられるでしょう。
このような要因を調べるには、色々な部門から人をたくさん集め、様々な有識者でブレインストーミングを行います。人の意見を否定したりしてはなりません。誰しも平等に発言権を与え、とにかく考えられえる要因をたくさん出しましょう。
グラフ
グラフには様々な種類が存在しますが、データを可視化することで数値の比較や変化をわかりやすくします。
グラフで可視化を行うことで、どのような内容がわかりやすくできるのか記載します。
- 折れ線グラフ(変動を見る)
- 棒グラフ(数量などを比較する)
- 円グラフ(比率を見る)
- 帯グラフ(比率を比較する)
- レーダーチャート(バランスを見る)
例えば、
折れ線グラフ:横軸を時間、縦軸を気温 ➡ 各時間毎の温度変化(変動)を可視化することができます。
棒グラフ:横軸を日付、縦軸を出荷数 ➡ 日々の出荷数量が比較しやすくなります。
円グラフ:部品の納入数と供給会社を可視化することで、会社毎の比率を可視化することができます。
帯グラフ:円グラフと同様ですが、一本の帯の形なので、比率が比較しやすくなります。
レーダーチャート:それぞれの項目ごとに比較しやすい形に可視化することができます。
数値データを可視化することで、全体像を把握しやすくしたりできる道具が『グラフ』です。
ヒストグラム
データの分布や最大値、ばらつきを把握しやすくします。
例えば、ここにネジ職人200名がいます。その中で、100名は新人さん、もう100品はベテランさんです。彼ら200名が部品を 2.5cm の長さに加工するとします。
その結果は…
どうでしょうか?
さすがベテランチーム、みんな 2.5cm 付近に仕上げてきました。対して新人チームは、何人かは2.5cmに仕上げることができましたが、まだ未熟なこともあり仕上がりはまばらですね。
このようにデータのばらつき具合や、一番多い値がわかりやすくなります。ヒストグラムは、データの分布を可視化することができます。
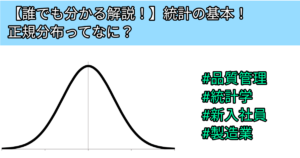
散布図
散布図で可視化することにより、2つの要因に関係性があるのかがわかりやすくなります。
X軸(横軸)とY軸(縦軸)調べたい2つの項目を入れ、データを点の集合で表します。
例えば、気温が上がるほど部品は変形しやすいか?幅が広くなるほど重みは増えるか?
といったように2つに関係性があるかどうかを調べます。
関係性がある場合を、『相関がある(相関関係にある)』といった表現を使いますが、
X軸が増えれば増えるほどY軸も増える事を『正の相関関係』といい、
X軸が増えれば増えるほどY軸は減る事を『負の相関関係』があるといいます。
図で表すとこんな感じです。
例えば、正の相関関係には『身長と体重(身長が高いと体重も重い)』『年齢と貯蓄(年齢を重ねると貯金も多い)』といったことが考えられます。
対して負の相関関係には『年齢と身長(年齢を重ねると身長は低い)』『気温とおでん販売量(気温が高くなるとおでんは売れない)』などが考えられます。
2つの要因に関係がない場合は、無関係の散布図のように無造作に点が打たれます。
チェックシート
チェックシートを事前に作っておくこおくことで、抜けや漏れ、忘れを防止し、正しい準備が整うようにします。
例えば、製造を始める前に、チェックシートに『作業台清掃』という項目を入れておき、清掃が終わったら☑するといったように運用します。
製造業では、装置の点検項目や何かの集計表でチェックシートが用いられます。
チェックシートの参考例を書いてみました。このようにエビデンス(証拠)として残しておくのも、品質を管理するうえで大切な取り組みの1つです。
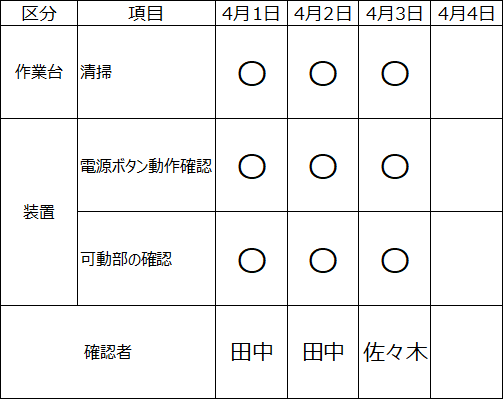
管理図
工程の状態を視覚し管理を適切に行うことで、安定した品質の製品を生産できるようにします。
管理図には、中心線(CL)を真ん中に引き、その上下に上方管理限界線(UCL)と下方管理限界線(LCL)を配置し、取得したデータを時系列で折れ線グラフとして表示します。
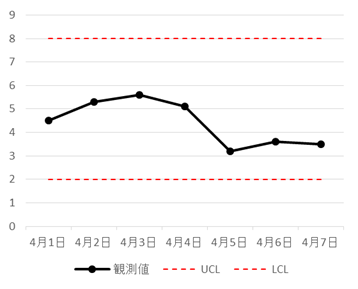
例えば、上図の例でいうと、日付別で温度状態を管理している図です。
2度以上8度未満で管理をするために、UCLとLCLを赤点線で示しました。そして、日々のデータを折れ線グラフで表します。万が一、温度状態が異常になったらいち早く気付き適切な状態に戻します。
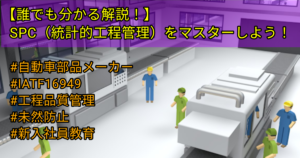
QC七つ道具を駆使して品質改善に取り組もう!
如何でしたでしょうか?この説明を理解頂ければQC七つ道具はマスターです!
品質改善において、数値データを可視化して状況を把握、分析することは必要不可欠です。QC七つ道具は、問題解決に向けたヒントを見つけやすくさせ、また問題を未然に防止することができます。
また、製造業の世界のみならず、日常生活にも役立てることができます。
例えば、家計簿をグラフで可視化したりすることで出費が多い原因を明確にすることができ翌月に対策を講じることができたり、旅行の忘れ物防止チェックシートを作成することで問題(忘れ物)を未然に防止できます。
このような活動を通し、ムダを無くすことで日々の品質改善に取り組んでいます。
まとめ
- QC七つ道具は、問題を未然に防いだり、問題を解決するヒントを探したりするための道具です。
- それぞれの道具が持つ特性を活かし、解決したい原因を探り改善を行うことで日々品質の向上に取り組んでいます。
- QC七つ道具は、製造業のみならず普段の生活にも活かせる知恵です。
コメント