当記事のリンクには広告が含まれています
ISO9001・IATF16949 第7章 支援
ISO9001 及び IATF16949 の第7章 は、以下の通りです。ここからが正念場になるので、是非一緒に頑張りましょう!
(下表の ”要求事項” の部分をクリックすると、解説ページにいけます。 )
ISO9001:2015 | 7 | 支援 |
ISO9001:2015 | 7.1 | 資源 |
ISO9001:2015 | 7.1.1 | 一般 |
ISO9001:2015 | 7.1.2 | 人々 |
ISO9001:2015 | 7.1.3 | インフラストラクチャ |
IATF16949:2016 | 7.1.3.1 | 工場、設備及び設備の計画 |
ISO9001:2015 | 7.1.4 | プロセスの適用に関する環境 |
IATF16949:2016 | 7.1.4.1 | プロセスの運用に関する環境 – 補足 |
ISO9001:2015 | 7.1.5 | 監視及び測定のための資源 |
IATF16949:2016 | 7.1.5.1 | 一般 |
IATF16949:2016 | 7.1.5.1.1 | 測定システム解析 |
ISO9001:2015 | 7.1.5.2 |
測定のトレーサビリティ |
IATF16949:2016 | 7.1.5.2 | 測定のトレーサビリティ(注記) |
IATF16949:2016 | 7.1.5.2.1 | 校正/検証の記録 |
IATF16949:2016 | 7.1.5.3 | 試験所要求事項 |
IATF16949:2016 | 7.1.5.3.1 | 内部試験所 |
IATF16949:2016 | 7.1.5.3.2 | 外部試験所 |
ISO9001:2015 | 7.1.6 | 組織の知識 |
ISO9001:2015 | 7.2 | 力量 |
IATF16949:2016 | 7.2.1 | 力量 – 補足 |
IATF16949:2016 | 7.2.2 | 力量 – 業務を通じた教育訓練 (OJT) |
IATF16949:2016 | 7.2.3 | 内部監査員の力量 |
IATF16949:2016 | 7.2.4 | 第二者監査員の力量 |
ISO9001:2015 | 7.3 | 認識 |
IATF16949:2016 | 7.3.1 | 認識 – 補足 |
IATF16949:2016 | 7.3.2 | 従業員の動機付け及びエンパワーメント |
ISO9001:2015 | 7.4 | コミュニケーション |
ISO9001:2015 | 7.5 | 文書化した情報 |
ISO9001:2015 | 7.5.1 | 一般 |
IATF16949:2016 | 7.5.1.1 | 品質マネジメントシステムの文書類 |
ISO9001:2015 | 7.5.2 | 作成及び更新 |
ISO9001:2015 | 7.5.3 | 文書化した情報の整理 |
IATF16949:2016 | 7.5.3.1 及び 7.5.3.2 | 7.5.3.1 及び 7.5.3.2 |
IATF16949:2016 | 7.5.3.2.1 | 記録の保管 |
IATF16949:2016 | 7.5.3.2.2 | 技術仕様書 |
第7章の支援では組織の品質マネジメントシステムが効率的にPDCAサイクルを回すために欠かせない支援プロセスに関しての要求事項が書かれています。
7.1.3.1 工場、施設及び設備の計画
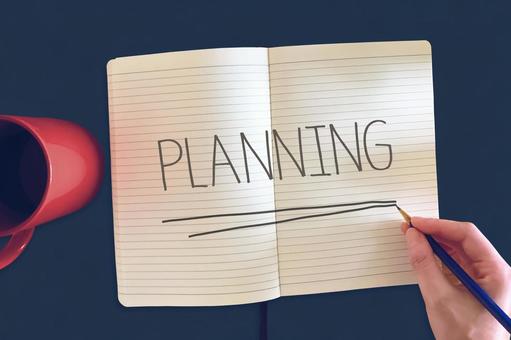
当該項目の、IATF16949要求事項のポイントを自分なりにまとめてみました。
組織は工場や施設及び設備の計画を作成する。また改善を行うために、リスクの特定や緩和の方法を、部門横断的チームを結成し検討する。
工場のレイアウトを検討する際には、組織は次の事項を考慮する必要がある。
① 材料や部品の流れや取り扱いを考慮し、現場のスペースに付加価値をつけられるように最適化し、不適合製品が流出しないように厳重に管理する。
② 該当する場合には、材料の流れがスムーズにいくよう考慮する。
新製品の工程設計時や、新しい製造フィージビリティが導入される際には、新しい方法(Method)を工程設計時に検討し、それが妥当なのか評価しなければならない。
なお、製造フィージビリティの評価には、必ず生産能力計画を含める必要がある。
これらの方法(Method)は、生産工程で変更が加わった際に行う評価においても適用ができるよう検討をする。
組織のリスクに対する定期的な再評価は、
以下の項目の変化点を含めた工程の有効性を維持する必要がある。
① プロセス承認
② コントロールプラン
③ 作業の段取り替え検証
製造フィージビリティの評価及び生産能力評価は、マネジメントレビューにて結果を報告し協議しなければならない。
注記1
これら要求事項は、原則的にリーン生産の適用望ましい。
注記2
これらの要求事項は、自社のサイトに協力会社が存在している場合は、組織と同様の計画に含め管理を行う。
用語の解説
ISO9001やIATF16949は国際規格であるため、原文は英語で構成されています。そのため、日本語に訳した際、少しわかりにくい表現で書かれているケースが多いです。まず初めに用語について解説をします。
部門横断的チーム
一言でいうと、色々な部門を集めて結成したチームです。IATF16949には時々出てくる用語になります。
工場を新しく立ち上げる際や、新しい設備を導入する際は、様々な部門の知見が必要です。例えば、生産工程を設計する生産技術部門や、出荷の数量を管理する生産管理、実際に作業を行う製造など、様々な視点や知見を集めリスクに備える必要があります。
ここの計画と似てIATF16949では、世の中の様々なリスクに備えるために「緊急事態対応計画」というものを定めるよう要求しています。気になる方は以下の記事も見てみてください。
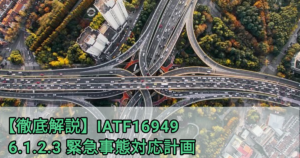
フィージビリティ
フィージビリティとは「実現性」「実現可用性」と訳され、ビジネス用語として使われています。
ISO9001での「実現性」とは、製造の「実現」と捉えてみてください。
製造をするためには、工場そのものの建屋や必要な工具•設備、材料や作業者のハンドリングや組み込む手順など、様々な支援を受け実現します。
方法(Method)
製造業においてとても大切な言葉です。4Mの1つで、(Man:人)(Machine:機械)(Material:材料)(Method:方法)を総称し4Mといいます。
Methodとは、簡単にいうと、設備の動かし方や、作業のやり方など製造をするための方法を示します。今のはミニマムな視点になりますが、例えば、製品の組み込み方(順番や工具の種類)、装置の設定方法などもMethodの要素です。
解説(計画の作成と検討)
新しく工場や設備を導入するときは、どこの組織も計画を立てるかと思います。いくらかかって、いつからいつまで何をするのか計画立てられますね。
その計画にはしっかりとリスクを考慮する必要があるとIATF16949は要求しています。そしてそのリスクを特定するため、部門横断的チームを結成し、協議をしなくてはなりません。これは、様々な知見を集めてリスクを特定するためです。
ここでいうリスクというのは色々と考えられますが、例えば、その設備で本当に能力が足りているか?供給数担保できるか? 工場を立てるうえで法律的手続きはないか?そもそも、その場所で良いのか?などが考えられるかと思います。
解説(工場レイアウトの考慮)
工場には必ずフロアレイアウトというものが存在します。どこにどういう設備が設置されており、どういう動線となっているのか可視化されています。このレイアウトは、新しい工場や設備を立ち上げる際や、既存の設備から新しい設備へ入れ替えを行うとき、設備を移動する際に作成します。
この要求事項は、レイアウトを作成・検討する際に考慮する項目が記載された要求事項です。
材料や部品の流れがスムーズにいかなければ、不具合を引き起こしたり、生産タクトが減少する原因のつながります。
1番のポイントとしては、レイアウトの検討段階から、不適合が流出しないよう考慮しなくてはならないことです。不適合品を管理する棚や場所は、生産品の流れから極力離れて、紛れ込まないように考慮することが必要です。
解説(妥当性評価)
工程設計時には、設備の設定方法や作業手順の方法などを妥当なのか検討する必要があります。
一般的にはDR(デザインレビュー)という場所で設計及び工程設計が妥当か様々なデータや結果をレビューします。
しかしながら、IATF16949では更に厳しいAPQPとい決まり事が定められています。
APQPに関しては、以下の記事で説明しているので、参考にご覧ください。フェーズ3というステータスで工程設計が述べられますが、必要なアウトプットが細かく規定されています。
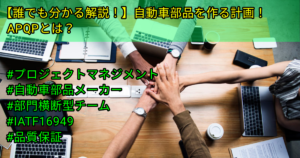
解説(生産能力計画)
製造フィージビリティの評価は、後に記述予定の「8.2.3.1 組織の製造フィージビリティ」にて詳しく解説する予定ですが、
簡単にいうと、顧客から「こういうものを作りなさい」と要求を受けている内容を実現できるのか、組織が検討・評価することです。
例えば、Specを満たせる製品を作り込む力が自社にはあるのか?お客様がお求めの数量をしっかり遅延なく納入することは可能なのか評価します。
生産能力計画とは、生産計画に対する工場での生産能力の妥当性をみるために行う計画のことをいいます。生産数量を担保できるような生産能力を兼ね備えているのか評価をする必要があります。
解説(工程変更への考慮)
解説(定期的な見直し)
工程の有効性を維持するためにリスクに対する定期的な再評価を行う必要があります。
この再評価には変化点を含める必要があり、例えば設備の新規導入によってコントロールプランが変更される際にも、リスクの再検証をする必要があるとIATF16949では要求しています。
ここでいう作業の段取り替え検証とは、日勤/夜勤の交代や休暇明けに稼働をしたり、作業の変更(条件や治工具変更など)や材料の切り替え(部品の入れ替え)などのタイミングに行う際の検証です。例えば、何かの検査機の設定値を変更した際、正しくない設定値であったら、不具合品をしっかりと検出できない可能性があるので、わざとNGサンプルを検査機に入れてNG判定をするのかチェックをしたりします。
このように変化点を含め、リスクの定期的な再評価を通し、高い品質保証体制を構築します。
解説(マネジメントレビューへの報告)
ここまでで、製造フィージビリティの評価や生産能力評価についてイメージはわいたと思いますが、これらの結果をマネジメントレビューで報告し、上位がいる場所でレビューを行います。
何故マネジメントレビューで報告しなくてはいけないかの理由は様々ありますが、計画段階できちんと顧客の要求に見合った製品を作り込めるのかトップマネジメントへインプットする必要があるためです。
組織のリソースを配分できるトップマネジメントがいる場でレビューすることで、開発の遅延や生産能力不足などといったトラブルの解消を期待できるでしょう。
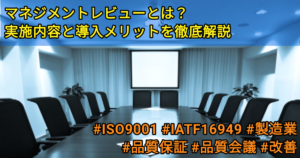
解説(リーン生産)
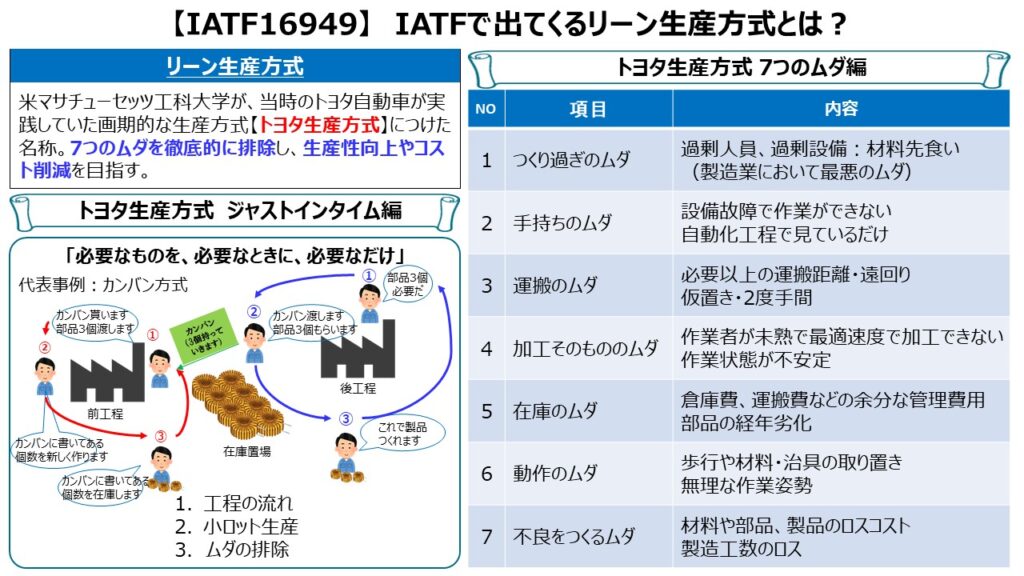
リーン生産とは、マサチューセッツ工科大学が1980年代に、当時トヨタが行っていた生産方法(トヨタ生産方式)を研究し体系化・一般化したものです。
奥深いものですが、ムダを排除して効率的な生産が可能なノウハウがたくさんあり、現在のサプライチェーンのベースを築き上げた生産方式です。
解説(サイト内の協力会社)
組織のサイト(工場や施設など)に入り込んで存在している、協力会社にも、同様の計画で管理を行う必要があるといっています。
例えば、自社工場の中に部品メーカーが並列して生産しているようなイメージをもってみてください。
代表例でいうと、テスラ工場の中でパナソニックがバッテリーを作っていたり、日産工場の中でマレリ(旧:カルソニックカンセイ)がモジュールを作っていたりすることです。
このような入り込んでいる協力会社へも、同様の計画で管理を行う必要があります。
コメント