当記事のリンクには広告が含まれています
ISO9001・IATF16949 第8章 運用
ISO9001 及び IATF16949 の第8章 は、以下の通りです。ここが、品質マネジメントシステムを運用するうえでの規定が書かれており、一番のメイン所になります。要求事項は長く続きますが、是非、一緒に勉強をしましょう!
(下表の ”要求事項” の部分をクリックすると、解説ページにいけます。 )
ISO9001:2015 IATF16949:2016 |
8 | 運用 |
ISO9001:2015 | 8.1 | 運用の計画及び管理 |
IATF16949:2016 | 8.1.1 | 運用の計画及び管理 – 補足 |
IATF16949:2016 | 8.1.2 | 機密保持 |
ISO9001:2015 | 8.2 | 製品及びサービスに関する要求事項 |
ISO9001:2015 | 8.2.1 | 顧客とのコミュニケーション |
IATF16949:2016 | 8.2.1.1 | 顧客とのコミュニケーション – 補足 |
ISO9001:2015 | 8.2.2 | 製品及びサービスに関連する要求事項の明確化 |
IATF16949:2016 | 8.2.2.1 | 製品及びサービスに関連する要求事項の明確化 – 補足 |
ISO9001:2015 | 8.2.3 | 製品及びサービスに関連する要求事項のレビュー |
IATF16949:2016 | 8.2.3.1 | ISO9001:2015 要求事項参照 |
IATF16949:2016 | 8.2.3.1.1 | 製品及びサービスに関連する要求事項のレビュー – 補足 |
IATF16949:2016 | 8.2.3.2 | 顧客指定の特殊特性 |
IATF16949:2016 | 8.2.3.3 | 組織の製造フィージビリティ |
ISO9001:2015 | 8.2.4 | 製品及びサービスに関する要求事項の変更 |
ISO9001:2015 | 8.3 | 製品及びサービスの設計・開発 |
ISO9001:2015 | 8.3.1 | 一般 |
IATF16949:2016 | 8.3.1.1 | 製品及びサービスの設計・開発 – 補足 |
ISO9001:2015 | 8.3.2 | 設計・開発の計画 |
IATF16949:2016 | 8.3.2.1 | 設計・開発の計画 – 補足 |
IATF16949:2016 | 8.3.2.2 | 製品設計の技能 |
IATF16949:2016 | 8.3.2.3 | 組込みソフトウェアをもつ製品の開発 |
ISO9001:2015 | 8.3.3 | 設計・開発へのインプット |
IATF16949:2016 | 8.3.3.1 | 製品設計へのインプット |
IATF16949:2016 | 8.3.3.2 | 製造工程設計へのインプット |
IATF16949:2016 | 8.3.3.3 | 特殊特性 |
ISO9001:2015 | 8.3.4 | 設計・開発の管理 |
IATF16949:2016 | 8.3.4.1 | 監視 |
IATF16949:2016 | 8.3.4.2 | 設計・開発の妥当性確認 |
IATF16949:2016 | 8.3.4.3 | 試作プログラム |
IATF16949:2016 | 8.3.4.4 | 製品承認プロセス |
ISO9001:2015 | 8.3.5 | 設計・開発からのアウトプット |
IATF16949:2016 | 8.3.5.1 | 設計・開発からのアウトプット – 補足 |
ISO9001:2015 | 8.3.6 | 設計・開発の変更 |
IATF16949:2016 | 8.3.6.1 | 設計・開発の変更 – 補足 |
ISO9001:2015 | 8.4 | 外部から提供されるプロセス、製品及びサービスの管理 |
ISO9001:2015 | 8.4.1 | 一般 |
IATF16949:2016 | 8.4.1.1 | 一般 – 補足 |
IATF16949:2016 | 8.4.1.2 | 供給者選定プロセス |
IATF16949:2016 | 8.4.1.3 | 顧客指定の供給者(指定購買 としても知られている) |
ISO9001:2015 | 8.4.2 | 管理の方式及び程度 |
IATF16949:2016 | 8.4.2.1 | 管理の方式及び程度 – 補足 |
IATF16949:2016 | 8.4.2.2 | 法令・規制要求事項 |
IATF16949:2016 | 8.4.2.3 | 供給者の品質マネジメントシステム開発 |
IATF16949:2016 | 8.4.2.3.1 | 自動車製品に関係するソフトウェア 又は組込みソフトウェアを持つ製品 |
IATF16949:2016 | 8.4.2.4 | 供給者の監視 |
IATF16949:2016 | 8.4.2.4.1 | 第二者監査 |
IATF16949:2016 | 8.4.2.5 | 供給者の開発 |
ISO9001:2015 | 8.4.3 | 外部提供者に対する情報 |
IATF16949:2016 | 8.4.3.1 | 外部提供者に対する情報 – 補足 |
ISO9001:2015 | 8.5 | 製造及びサービス提供 |
ISO9001:2015 | 8.5.1 | 製造及びサービス提供の管理 |
IATF16949:2016 | 8.5.1.1 | コントロールプラン |
IATF16949:2016 | 8.5.1.2 | 標準作業-作業者指示書及び目視標準 |
IATF16949:2016 | 8.5.1.3 | 作業の段取り替え検証 |
IATF16949:2016 | 8.5.1.4 | シャットダウン後の検証 |
IATF16949:2016 | 8.5.1.5 | TPM(Total productive maintenance) |
IATF16949:2016 | 8.5.1.6 | 生産治工具並びに製造, 試験, 検査の治工具 及び設備の運用管理 |
IATF16949:2016 | 8.5.1.7 | 生産計画 |
ISO9001:2015 | 8.5.2 | 識別及びトレーサビリティ |
IATF16949:2016 | 8.5.2.1 | 識別及びトレーサビリティ – 補足 |
ISO9001:2015 | 8.5.3 | 顧客又は外部提供者の所有物 |
ISO9001:2015 | 8.5.4 | 保存 |
IATF16949:2016 | 8.5.4.1 | 保存 – 補足 |
ISO9001:2015 | 8.5.5 | 引き渡し後の活動 |
IATF16949:2016 | 8.5.5.1 | サービスからの情報のフィードバック |
IATF16949:2016 | 8.5.5.2 | 顧客とのサービス契約 |
ISO9001:2015 | 8.5.6 | 変更の管理 |
IATF16949:2016 | 8.5.6.1 | 変更の管理 – 補足 |
IATF16949:2016 | 8.5.6.1.1 | 工程変更の一時的変更 |
ISO9001:2015 | 8.6 | 製品及びサービスのリリース |
IATF16949:2016 | 8.6.1 | 製品及びサービスのリリース – 補足 |
IATF16949:2016 | 8.6.2 | レイアウト検査及び機能試験 |
IATF16949:2016 | 8.6.3 | 外観品目 |
IATF16949:2016 | 8.6.4 | 外部から提供される製品及びサービスの検証及び受入れ |
IATF16949:2016 | 8.6.5 | 法令・規制への適合 |
IATF16949:2016 | 8.6.6 | 合否判定基準 |
ISO9001:2015 | 8.7 | 不適合なアウトプットの管理 |
IATF16949:2016 | 8.7.1 | 8.7.1 |
IATF16949:2016 | 8.7.1.1 | 特別採用に対する顧客の正式許可 |
IATF16949:2016 | 8.7.1.2 | 不適合製品の管理 – 顧客規定のプロセス |
IATF16949:2016 | 8.7.1.3 | 疑わしい製品の管理 |
IATF16949:2016 | 8.7.1.4 | 手直し製品の管理 |
IATF16949:2016 | 8.7.1.5 | 修理製品の管理 |
IATF16949:2016 | 8.7.1.6 | 顧客への通知 |
IATF16949:2016 | 8.7.1.7 | 不適合製品の廃棄 |
第8章の運用では、組織の品質マネジメントシステムを実際に運用するためのプロセスについての要求事項が書かれています。ご覧の通り、ISO9001では不足していると判断し、IATF16949でたくさんの要求事項が追加されています。
8.3.5.1 設計・開発からのアウトプット – 補足
IATF16949要求事項のポイントを自分なりにまとめてみました。
はじめに
当該要求事項にも出てきていますが、FMEAや特殊特性といった用語はIATF16949要求事項に度々出現する用語となります。
これらに関しては、詳細の説明記事を作成したので、不安な方は参考にしてみてください。
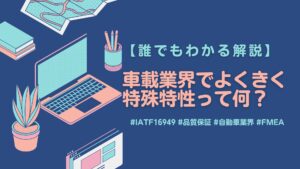
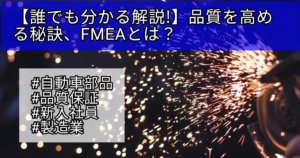
解説(インプットとの整合性)

なお、製品設計・開発へのインプットと対比させる必要があるので、参考にインプットに関する要求事項も掲載いたします。

解説(FMEAの結果)
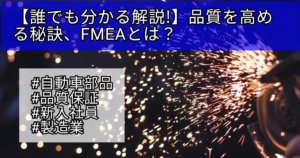
解説(信頼性調査結果)
解説(特殊特性)
解説(DFSS、DFMA、FTA)
DFSS(シックスシグマ設計)
シックスシグマ設計の定義は、顧客の期待を満たし、シックスシグマ品質レベルで生産可能な、確かな設計とすることを狙いとする、体系的方法論や、ツール、手法を示す。
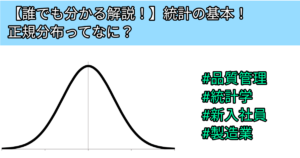
徹底的な作りこみを開発・設計段階から行うことを指し、Define(機会の定義)、Measure(問題の測定)、Analysis(分析)、Design(設計)、Verify(検証)のステップで進めていきます。
なぜなぜ分析、実験計画法、回帰分析、重回帰分析およびQC7つ道具等を駆使し、顧客要求に見合った製品を設計する体系的な手法となります。
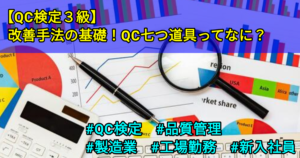
DFMA(製造及び組立設計)
DFM(製造設計)とDFA(組立設計)が組み合わさった設計方法論を示す。
DFMは、より容易に生産するための設計最適化を目指すプロセスである。DFMは、不具合のリスクを低減したり、コストを下げたり、組立てがしやすくするための設計最低化を示します。
両者が組み合わさった設計手法の方法論が、DFMAと呼ばれます。
FTA(故障の木分析)
システムの望ましくない事象を解析するための手法。故障の木は、システム全体の論理図を作図することで、故障自体や、サブシステム尚の設計的要素と、故障事象との関係性を結び描く手法です。
故障とシステムの因果関係や、故障に繋がる要因を分析する際に用いられる手法です。
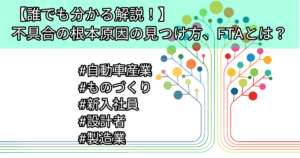
解説(3D、2D図面および幾何学寸法公差)
3Dモデルとは、3次元空間上に、立体的な形状を表したツールであり、一般的には3DCADと呼ばれます。2D図は、平面上に作図された図面で、回路図面や展開図面、構造図等を示します。
幾何学寸法公差とは製図用語であり、幾何学的な形状や姿勢、位置からずれることが許される領域をいう。交差は、図面の中に特別な枠を設け、その中に交差値を記入し、指示箋を明記することで、位置関係と数字関係を結びつけます。
解説(DRの結果)
解説(アフターサービス)
解説(サービス部品)
(約20年がオーソドックスな契約かと思われます)
(実際は、直接オーダーを受けたりすることもありますが、割愛します)
解説(梱包・ラベリング)
解説(注記)
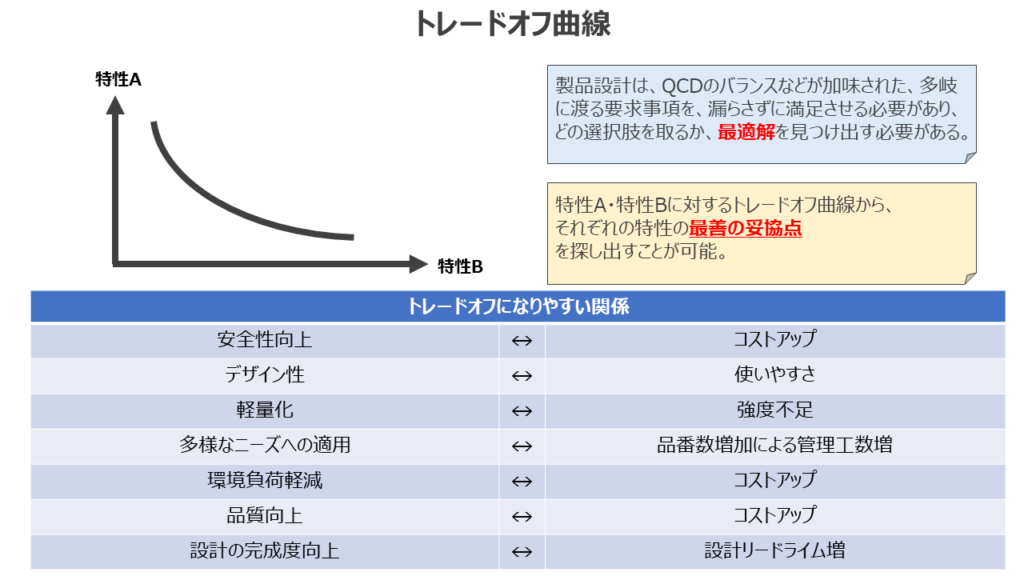
トレードオフ曲線とは、製品の様々な設計特性の関係を理解し、伝達するためのツールとなります。
1つの特性に関する製品性能を縦軸に、もう一つの特性を横軸都市、それから二つの特性に対する製品性能を示す曲線がプロットされ、最善の妥協点(最適解)を見つける1つの手法です。
このようなプロセスを通して、解決された問題があれば、設計開発のアウトプットに含めることが望ましいと規定されています。
コメント